Nine Steps to Prevent On-The-Job Injuries at Your Brewery
When an employee gets hurt, it is expensive for everyone. The employee may miss work during recovery from the accident. The brewery, meanwhile, must find ways to cover the schedule of the missing worker or suffer downtime and, by default, loss of production and revenue.
That is why, from a pure cost perspective, reducing the odds of on-the-job injuries is one of the most profitable things a brewery can do. Here are 9 steps you can take to maintain control of lost time accidents.
1. Automate Processes/Movements
A repetitive motion injury for example, is caused by constant lifting or doing the same movements over and over for hours. They are often quite painful and may take weeks to heal. Breweries should automate processes as soon as economically feasible to relieve workers from such motions. In the meantime, ensure your workers have ample opportunities for alternating duties when feasible.
2. Prevent Back Injuries
Back injuries…you’ll pay big downtime to an employee who injures their back due to improper lifting or lifting too much. It’s such a common hazard in breweries. Set and enforce strict policies regarding two-person lifts, and offer mandatory lift training for workers. If appropriate, consider utilizing back braces, but don’t let those substitute for proper lift protocols.
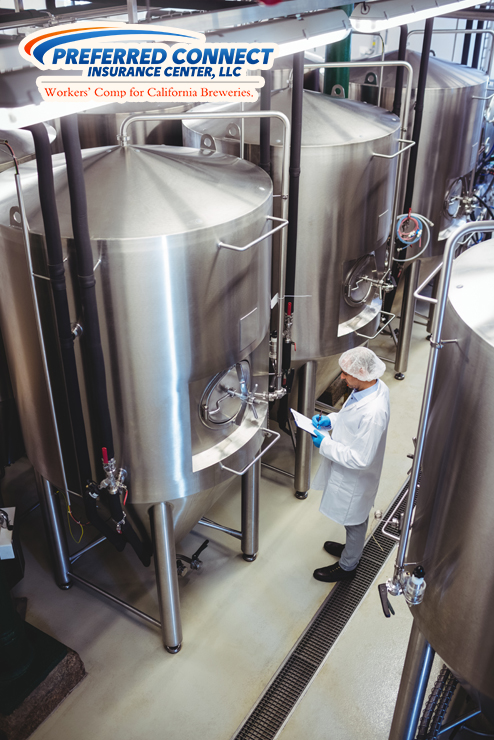
3. Maintain a Clean Floor Rule
Wet floors are accidents waiting to happen. If you know of a spill, mark it with appropriate signage and get it cleaned up ASAP...before someone slips and breaks a wrist. Simple common sense housekeeping will help keep clutter off the floors, before someone trips face first and busts a nose.
4. Make Your Stairs Slip-Proof
Want a very expensive on-the-job injury added to your business costs? Allow for slippery staircases.
Workers need to always be cautious climbing up or down stairs. Investing in slip resistant step treads will pay dividends by reducing the risk of falling. And if you have any elevated areas in need of handrails, get them installed as soon as possible.
5. Train the Forklift Operator
Forklifts are vital tools but drivers can easily get overly confident in their own skills, driving too fast in small spaces or zipping around corners. An overturned forklift or a crash into equipment or another worker is a very serious risk. Accept no horseplay and ensure all drivers are properly trained before getting behind the wheel. Additionally, make sure to keep up diligent daily inspection logs of the equipment.
6. Handle Beer Kegs with Special Care
For starters, kegs are heavy, which is why steel-toed shoes are advised! They can also be pressurized, and must always be treated with special care. They are rated to withstand extreme pressure but this does not mean they are automatically safe to be around. Kegs containing pressurized air are essentially stainless steel rockets.
Special Alert: Never allow a non-trained/non-expert to attempt to de-dent a damaged, pressurized keg, and never tamper with keg safety devices.
7. Manage Heat and Steam Hazards
Heat and steam hazards must be taken very seriously. Pipes should be inspected for proper insulation. Potentially hot surfaces must be labelled in accordance with OSHA guidelines and physical guarding should be installed to safeguard against inadvertent contact with personnel. Meanwhile workers near these areas should be wear appropriate long-sleeved or long-legged garments and provided with proper protective equipment such as goggles and gloves.
8. Be Proactive in Identifying and Fixing Problems
If you see a problem, fix it! If it can be fixed on the spot, take the time to do it. Or if it can’t, mark the area with a sign or tag then immediately report it for attention. There should be zero tolerance for risks which are seen but ignored. Along the same line, hold frank and open discussions with coworkers, supervisors, and management about suggestions for improving workplace safety.
9. Keep Track of Safety Issues Until They Are Resolved
Use existing Cal/OSHA safety checklists to identify problem areas, then actively track how the fixes are going. Setting up deadlines for completion can help ensure work gets accomplished sooner rather than later.
The Bottom Line
Develop a ‘culture’ of safety in every area your brewery, and don’t allow shortcuts or carelessness to creep in. Invest in worker education and workplace safety awareness, hold employees accountable...and commit to keeping every employee safe all the time. There’s no way to ensure 365 days without an on-the-job accident...but that should be the goal to aim for.